Blogtext
Sieves and Mills - Flexible Use in (Almost) Any Process Situation
Conical mill/conical sieving machine:
Conical mills or conical sieving machines are used for uniform size reduction of pharmaceutical active ingredients. Furthermore, they can also be used for blending, sieving, and dispersing. They are available in a variety of dimensions – from laboratory scale through to systems with a high capacity.
Compared to other crushing technologies available on the market, the sieve offers numerous advantages for production: A lower noise level, narrow particle size distribution, high design flexibility and higher capacity. This means that for the processing of low-density materials, a sieving system of this type can achieve a throughput that is 50 % higher than that of conventional mills.
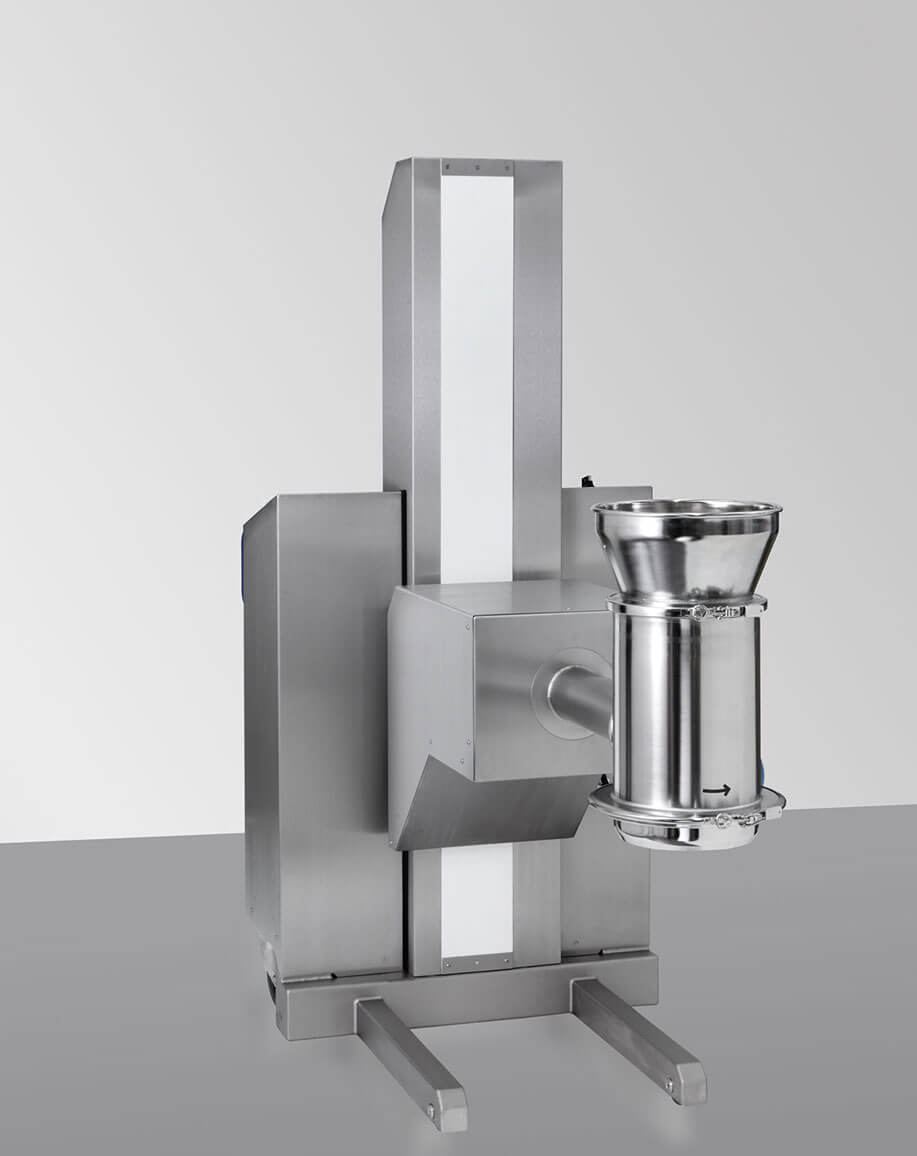
The patented BTS Turbo sieve by L.B. Bohle Maschinen und Verfahren GmbH (Ennigerloh) is used for calibrating the particle size and thus guarantees an optimal particle size distribution.. The use of various conical sieve inserts (hole sieves and friction sieves) supports the processing of both dry products and wet products at speeds of 150 to 1500 rpm (revolutions per minute).. This makes it possible to achieve product capacities of two to three metric tons in one hour.
Operators work with an easy-to-use 7“touch panel that provides access to user management and recipe management as well as PDF batch print management and includes a USB interface. The explosion-proof version of the Turbo Sieve can also be used for applications where compliance with the ATEX directives is required..
The easy-to-clean design of the sieve makes manual cleaning quick and convenient. The sieve container is easy to remove using the combination of bayonet mount and clamp ring.
This makes it very easy to clean the individual components. As an option, the sieve housing can be equipped with cleaning nozzles for simple WIP cleaning where material residue is quickly removed from inside the sieve container. Cleaning nozzles on the sides of the sieve insert and below the angled drive are included in the scope of supply. They receive the cleaning fluid from a central water connection point.
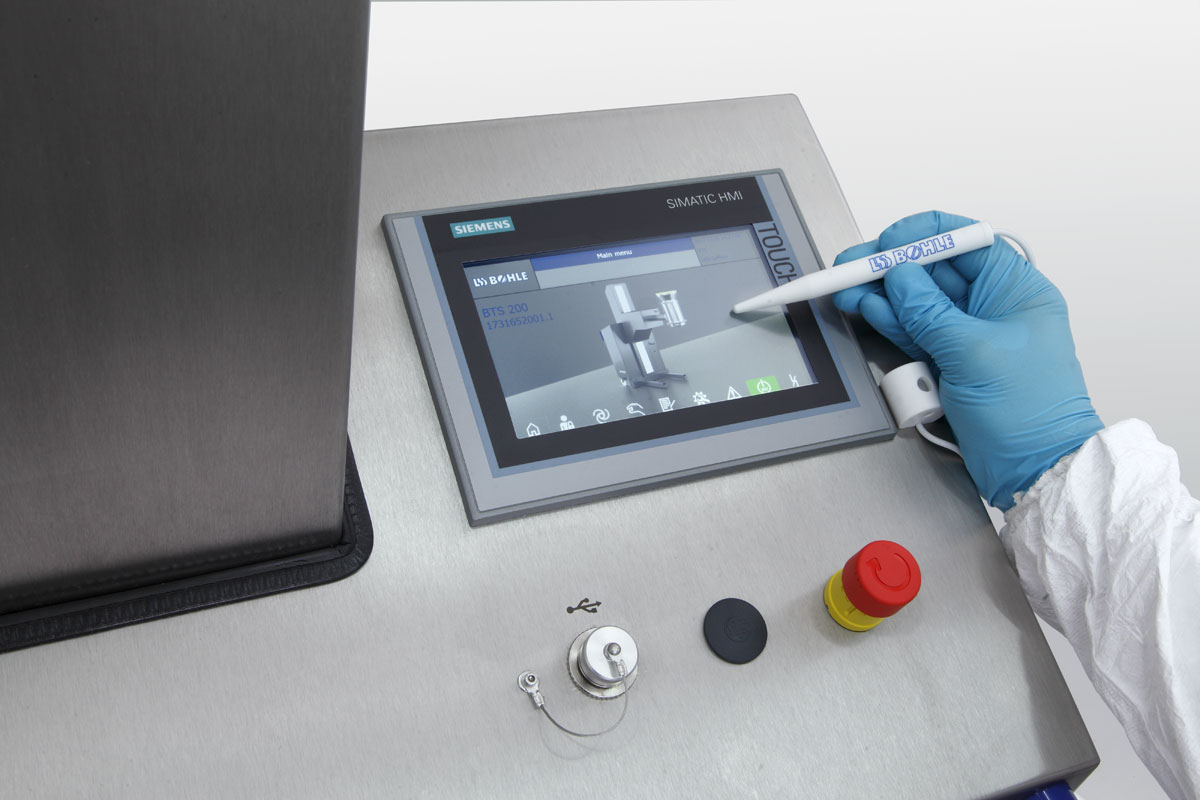
Hammer mills
Hammer or turbo mills are suitable for research and development, as well as for batch production or continuous manufacture. They are used for the milling of powders, agglomerates, and granules. Hammer mills are used in particular if the application demands a precise particle reduction for hard-to-mill active ingredients and other substances. In addition, hammer mills are used to re-mill fragmented tablets..
Tablets that have already been produced undergo inspection and may fail to meet the customer’s requirements for various reasons. Criteria for this include incorrect hardness, optical defects, or a deviating weight. If the tablet does not fulfil the specifications, the manufacturer can use the hammer mill to pulverize the tablets again and re-use the materials. The re-milling of the tablets and the recycling of the materials in production ultimately reduces the rejects rate and increases productivity..
BTM (Bohle Turbo Mill) hammer mills can reach speeds between 600 rpm and 6000 rpm and produce up to 1,500 kg/h. In order to achieve this, the BTM is equipped with an automatic dispenser unit (rotary feeder). This allows the operator to feed the material into the milling chamber evenly and without overloading. In addition, such automatic feeder devices can control the powder flow in the milling chamber. Other benefits: Less heat is generated, and the process can be repeated using the same parameters.
The internal rotor has two sides with different functions that support applications with wet or dry products. The knife side chops sticky products. The hammer side is used for crushing hard, crystalline products.
In the hammer mill, the particle size is defined by the sieve size selected for the mill. The BTM provides different sieve inserts that can be used to reduce the material size to as little as 0.1 mm.
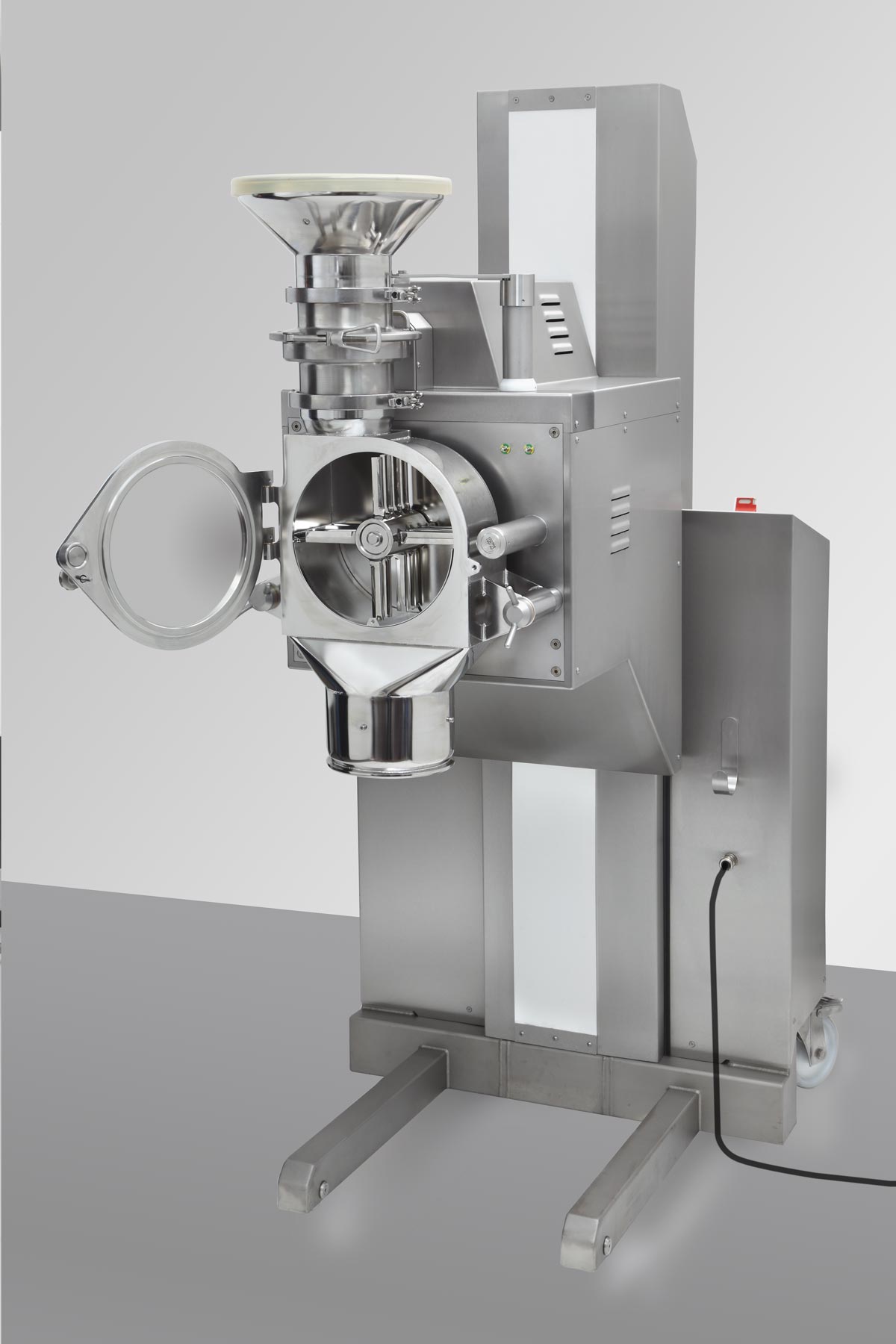
An application example
Developers of cell cultures used to use ball mills to reduce the particle size of initial blends. Ball milling is time-consuming. It is based on ceramic balls in a tumbling container that crush the products into powder.
After grinding of a batch, the mill and hundreds of ceramic balls inside must be cleaned. This cleaning process can take up to a week. The machine cannot be used during this time. It is not available then if a customer requests, for example, a customized, fast powder batch.
A manufacturer of such cell cultures was looking for a mill with which he would be able to meet the requirements of his biopharmaceutical customers more flexibly and efficiently. The mill also had to have a smaller footprint and needed to be mobile. It was to be possible to remove the device from the original production room for cleaning in order to clear space for further production steps.
The customer also had product-specific requirements for the mill in terms of temperature, particle and batch sizes. Cell cultures require small particles for perfect dissolution rates. Up to 50 percent of the batch must be smaller than 100 micrometres. Beyond this, the medium is highly susceptible to temperatures above 37°C since the powder loses bioactivity at these temperatures.
After probing the market, the producer contacted L.B. Bohle for some grinding trials. With the BTM 150 Turbo Mill, L.B. Bohle achieved the desired product size at a throughput of 375 kg/h in a closed container-to-container grinding system (inline process). For the test, the Bohle experts chose a rotor speed of 6000 rpm with the hammer side of the rotor.
After a production cycle of 30 kg, a temperature of approx. 30 °C was measured. The grinding chamber was equipped with a cooling jacket to better control the temperature, discharge the resulting heat and meet the manufacturer’s specifications. In order to prevent condensation caused by cooling in the grinding chamber, nitrogen will be introduced into the grinding chamber and discharged again by the filter.
In addition, a 1-millimeter sieve insert was used in the turbo mill to ensure identical particle size as in the ball mill.
The precise results of the BTM convinced the manufacturer of this solution. He first ordered one hammer mill, and later followed up with four more. Installation of the mills allowed the manufacturer to significantly increase his processing efficiency. Several batches (e.g. 1000 kg-batches) can now be ground per week instead of one or two (as with the conventional ball grinding method), since the BTM can be disassembled and cleaned very quickly almost without any tools.