Blogtext
Roller Compactor - flexible and highly efficient
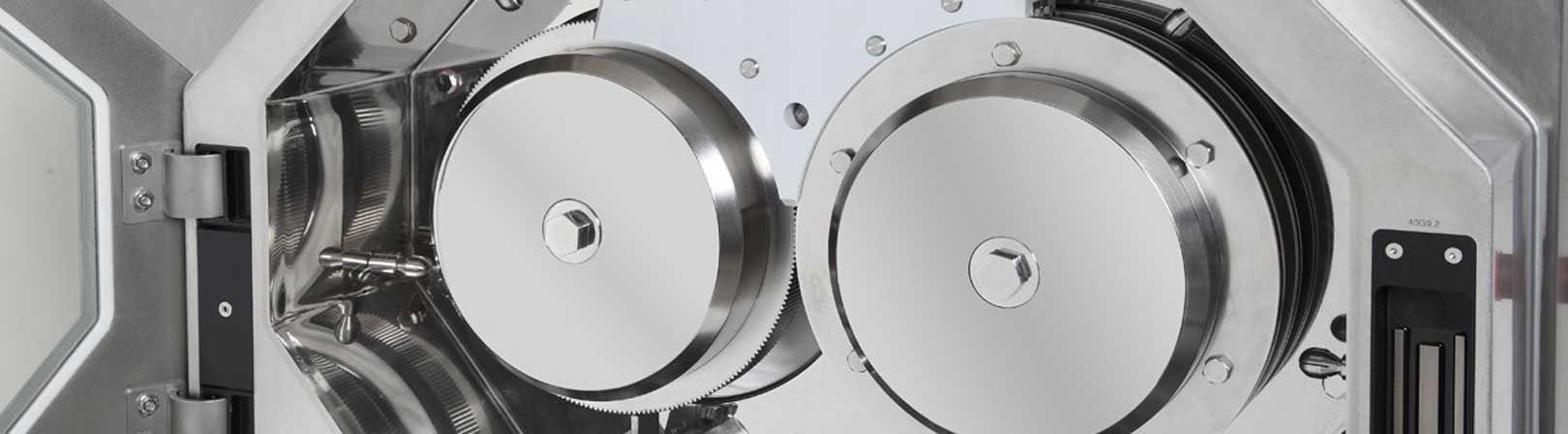
Roller compaction, also known as dry granulation, has become a widely used granulation technology in recent years. It has a wide range of applications. Powders are compacted between rotating rollers to form a flake. The flakes are crushed into granules with the desired particle size distribution using a sieve and sieve inserts. The pressed and dried granules are used in various ways in the pharmaceutical industry. Granules can be used as starting materials, intermediates, dosage forms for immediate preparation, and granules for ingestion.
Compared to the starting material, compacted granules have a higher bulk density and a larger particle size. As a result, the granules have better flow properties, which means better processing. Granulation also reduces dust and fines. This results in little or no material loss and low dust exposure. Agglomerates pre-compacted by roller compaction are easier to tablet than powders. All of the properties of compacted granules support the tableting goal of producing a tablet that is as uniform as possible.
Unlike wet granulation, which is a continuous process, roller compaction is a well-established process in the production of solids. Roller compaction is particularly suitable for moisture-sensitive pharmaceutical substances. A key advantage of roller compaction is that no energy is required for drying and solvent recovery. This is a decisive argument in favor of roller compaction, especially in times of high energy costs.
Horizontal roll arrangement with advantages
A roller compactor is distinguished by the arrangement of the rolls. There are systems with horizontal, vertical, and inclined rolls.
L.B. Bohle (Germany) uses horizontal rolls for their roller compactor. This arrangement has the advantage that the screws are better ventilated, and the flakes are discharged over a short distance.
Other features of roller compactor:
The systems also differ in whether the gap is fixed or variable. A roller compactor with a variable gap is preferred. This is the only way to ensure constant pellet porosity at a constant pressing force and thus reproducible flake production. During continuous measurement of the gap distance, a comparison is made between the actual and target values. The goal is to always maintain a parallel gap between the rolls during the process so that the exiting flake has identical properties across the entire width.
In addition, the screw speed is linked to the gap adjustment in a control loop. As a result, when the nip opens, less material is conveyed by the screw into the nip, allowing the nip to close again. The automatic control produces flakes of defined thickness and porosity.
Electromechanical drive
L.B. Bohle’s BRC series combines high product capacity with minimal material loss. In contrast to competitive hydraulic systems, the force generation is purely electromechanical. This ensures consistent scab characteristics. The electromechanical drive eliminates the disadvantages of hydraulic control, such as aging of the oil and control valves, as well as temperature fluctuations and contamination of the oil. This high-precision process is further supported by the use of force-measuring sensors located inside the force adjustment to directly measure the press force. The results are more accurate than in hydraulic systems where the values are usually calculated.
The roller compactor controls the compaction force and flake thickness in a very innovative way, producing uniform compaction of the material over a production range of < 1 – 400 kg/h. At the same time, the ingenious – innovative machine design facilitates handling and shortens the assembly procedure.
The hygienic design and the standard integrated washing nozzles guarantee an effective WIP process with residue-free removal of the product. In addition, with its functional GMP-compliant design and the possibility of PAT tool implementation, the roller compactor meets the requirements of the “Quality by Design” concept.
In addition to the compaction force, the size reduction step has a significant influence on the final particle size of the granules. The Bohle Conical Turbo Screen Mill BTS and its screen inserts ensure gentle size reduction of the flakes into granules with the desired particle size distribution – even at high material throughputs. At the same time, each BRC can be converted to an alternative rotary screen BRS in a matter of minutes, allowing it to be flexibly adapted to process and flake requirements.
Roller Compactor in practice
L.B. Bohle has been producing its BRC roller compactor range since 2012, and over the years the number of products manufactured via roller compaction has increased significantly worldwide, as this granulation method is very economical. Roller compaction is a continuous process, achieves high throughput, requires little space and energy, and has the advantage of not requiring granulating fluids and drying equipment.
A roller compactor can be used for a wide range of products. Many generic drugs are dry granulated, such as ibuprofen, metformin, blood pressure medications and antibiotics. Increasingly, new products are being developed using roller compaction from the outset.
Although roller compaction is a continuous manufacturing process suitable for both large and small batch sizes, almost all products are currently manufactured in batches.
Change Over: Due to its innovative design (ergonomic height, no ladder or framework needed) the changeover is time saving. Changeover after cleaning and re-assembling can be done in 30 min. Competitors systems require cleaning and assembly times up to 8 hours. At the BRC roller compactor only minimum tools are necessary (at roller and scrapper) all other components are designed for tool less changeover.
Roller Compactor with highest flexibility – versatile integration in the production process
A major advantage of the roller compactors is their small footprint and flexible integration into the production process. Numerous machines are installed in various production scenarios for batch and continuous manufacturing. Solutions can be found as stand-alone systems, wall-mounted installations, applications on platforms as well as over several floors, interlinked systems, and containment applications.
Containment – no problem
Especially in new products the active pharmaceutical ingredients (APIs) are becoming increasingly more potent. In some markets, the segment for high potency active pharmaceutical ingredients (HPAIs) is growing in the double-digit range, especially driven by oncology medication.
In addition to requirements set by manufacturing guidelines, it is essential that the product is safe for the machine operator and, of course, for the patient. As a result, companies are faced with new challenges in all toxicity classes in which customers want to use plants and processes.
So, a special version for containment applications for containment level OEB 5 is shown as an example.
The containment roller compactor version includes:
- Integrated isolator unit in the compacting unit with corresponding vacuum monitoring
- Glove box with safety request for flake removal
- Containment port for flake sample collection
- Containment port underneath the sieve unit for the removal of granules
- Convenient access as no complete isolator unit is installed around the entire compactor
- Residue-free removal of product with integrated WIP equipment (WIP is also integrated in the standard version).