Einstieg
Efficient and gentle granulation
Dry granulation for tablet production
Dry granulation, also known as roller compaction, is a proven granulation process used primarily in the pharmaceutical industry, but also in other sectors (chemicals, food, nutraceuticals). Unlike wet granulation, dry granulation does not require the use of liquids.
In dry granulation, the granules are formed directly from the powdered raw materials using mechanical pressure. As no liquids are added, the energy- and cost-intensive drying process is not required. This makes dry granulation a particularly effective and economical solution, especially for raw materials that are sensitive to moisture or heat.
Dry granulation also offers the possibility of improving the physical properties of powders and adapting them to the requirements of further processing. Parameters such as flowability, density, porosity and particle size are optimised. The continuous dry granulation process combines compaction and the subsequent grinding step (sieving/calibration) to ensure a high quality and Dry granulation, also known as roller compaction, is a proven granulation process used primarily in the pharmaceutical industry, but also in other sectors (chemicals, food, nutraceuticals). Unlike wet granulation, dry granulation does not require the use of liquids.
In addition to continuous dry granulation, L.B. Bohle dry granulators are also suitable for batch production, either as a stand-alone machine or integrated into a continuous production line.
However, batch production with separation of the production steps is more suitable for smaller quantities and requires more time and resources than dry granulation in continuous production.
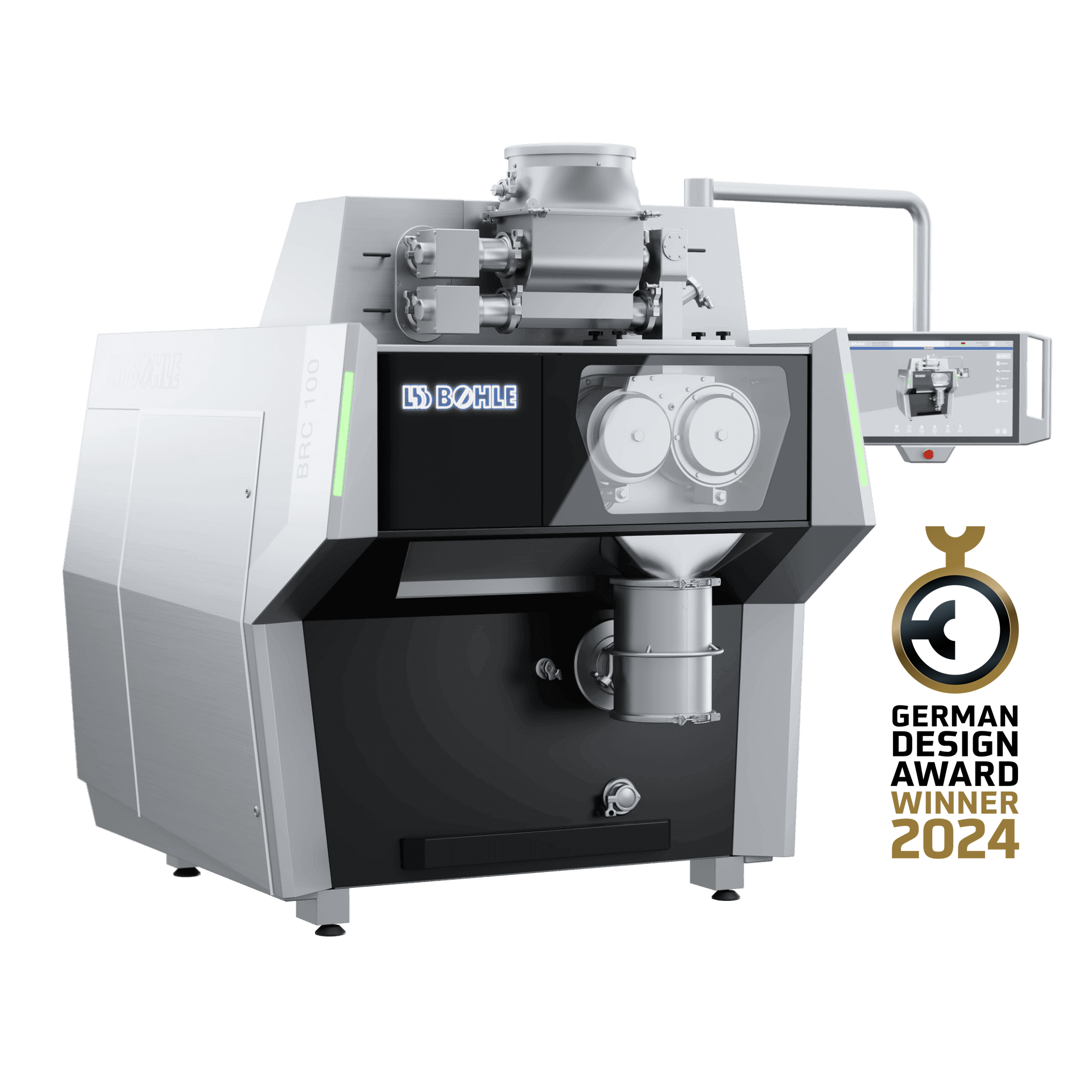
Containment applications
Containment applications for dry granulation
To ensure operator safety and the best possible product quality during dry granulation, L.B. Bohle offers suitable containment solutions. These are particularly essential when handling sensitive, hazardous and highly potent active ingredients. The aim is always to achieve an optimum balance between maximum safety, efficiency and cost.
The BRC series dry granulators offer not only comprehensive protection, but also options for a wide range of interfaces. In a customer-specific application, the system is filled via a lifting column and a containment valve. The valves are removed ergonomically and safely via glove access with safety interrogation. Product samples can also be taken at any time via two containment ports.
Trennbild
Applications of dry granulation
Applications of dry granulation beyond the pharmaceutical industry
Dry granulation is not only an indispensable process in the pharmaceutical production of tablets, capsules and other dosage forms, but has also proved its effectiveness in other industries. In particular, dry granulation is often the preferred method for large-volume or moisture-sensitive products. It therefore plays a central role in the processing and optimisation of powdered raw materials in the following industries
In the food and nutraceutical industries, dry granulation is used to process powdered raw materials such as sugar, starch, milk powder, instant drinks, soups, vitamins and minerals.
The chemical industry uses dry granulation when powders with specific physical properties are required. Catalysts, fertilisers, paints and pigments require specific granulations. In the cosmetics industry, dry granulation is used to granulate raw materials: e.g. face powder, blusher or eye shadow. These products are very sensitive to moisture.
In recycling and waste management, dry granulation is used to convert waste products such as metal powder into manageable granules. The building materials industry uses dry granulation to process raw materials for the production of cement, lime or gypsum.
Industries
Industries using dry granulation
- Pharmaceutical Industry
- Chemical Industry
- Food Industry
- Food supplements
- Cosmetics Industry
- Recycling & Waste Management
- Building Materials
Advantages
The process: Advantages of dry granulation
Dry granulation offers many advantages, especially when processing sensitive raw materials. For example, dry granulation is used for large-volume or moisture-sensitive products.
![]() |
Optimum pellet quality (flowability, compressibility and stability) |
![]() |
Precise process control (control of compaction pressure, roll speed and feed) |
![]() |
High product capacity |
![]() |
Improved compressibility/flow properties |
![]() |
Gentle material handling (minimised material abrasion) |
![]() |
Consistent flake properties |
![]() |
Quick and easy scalability |
![]() |
Continuous process |
![]() |
Minimal material loss |
![]() |
Small footprint |
![]() |
Favourable drying process as it is not energy intensive |
![]() |
Particularly suitable for large volume or moisture sensitive products |
![]() |
Proven process for decades |
![]() |
Meets GMP (Good Manufacturing Practice) requirements |
Trennbild 2
Advantages 2
Advantages of dry granulators from L.B. Bohle
![]() |
Oil-free electro-mechanical drive ensures stable compaction and low energy consumption; different screen configurations (conical / oscillating) provide flexibility of use |
![]() |
Effective WIP (Washing in Place) as standard |
![]() |
Quick assembly / disassembly of the system in less than 10 minutes (virtually tool-free) |
![]() |
Easy integration into other systems (interlinked systems) or continuous production systems |
![]() |
Hygienic design for optimum process reliability, easy cleaning and ergonomic operation |
![]() |
Fast installation: flexible, mobile plug & play machine |
![]() |
Reliability and durability reduce downtime and maintenance costs |
![]() |
Transparent costs: |
![]() |
All components mounted in the system, no separate control cabinet required |
![]() |
No additional assembly tool required for rollers |
![]() |
No oil consumption or oil change required |
![]() |
High transparency for maintenance and calibration (can be done independently) |
You can download our product brochure on granulation with the Roller Compactor / dry granulator here:
Go to the product brochure
Differences
Differences between dry granulation and wet granulation
Unlike wet granulation, which requires liquids, dry granulation does not use solvents or water. This not only reduces process times, but also the risk of raw material degradation. Dry granulation is also more environmentally friendly as it does not use solvents that have to be disposed of or recycled. Dry granulation also eliminates the need for energy-intensive drying.
L.B. Bohle offers technologically leading solutions for dry and wet granulation. With its extensive expertise in the various processes, L.B. Bohle has the optimum system for every process. Whether you are dealing with large batches or development processes, we have the systems to make your dry or wet granulation more efficient and productive.
- Lower material, labour and energy costs in dry granulation
- Less space required and faster processes in dry granulation (less GMP space required, plug & play machine)
- Use of liquids and solvents only in wet granulation
- For wet granulation, the batch size must be adapted to the capacity of the machine – not for dry granulation
- Less equipment required for dry granulation than for wet granulation
Read more

Learn more about granulation solutions
Granulation technologies and machines are one of the most relevant processes in the pharmaceutical industry for the production of medicines and pharmaceuticals.
Learn more about granulation
The L.B. Bohle granulation systems for dry granulation and wet granulation:
To the granulation systems
Bildergalerie
Contact
Your contact for dry granulation
Steve Chahidi
Area Sales Manager
inquiry@lbbohle.de
+49 2524 – 93 23 0
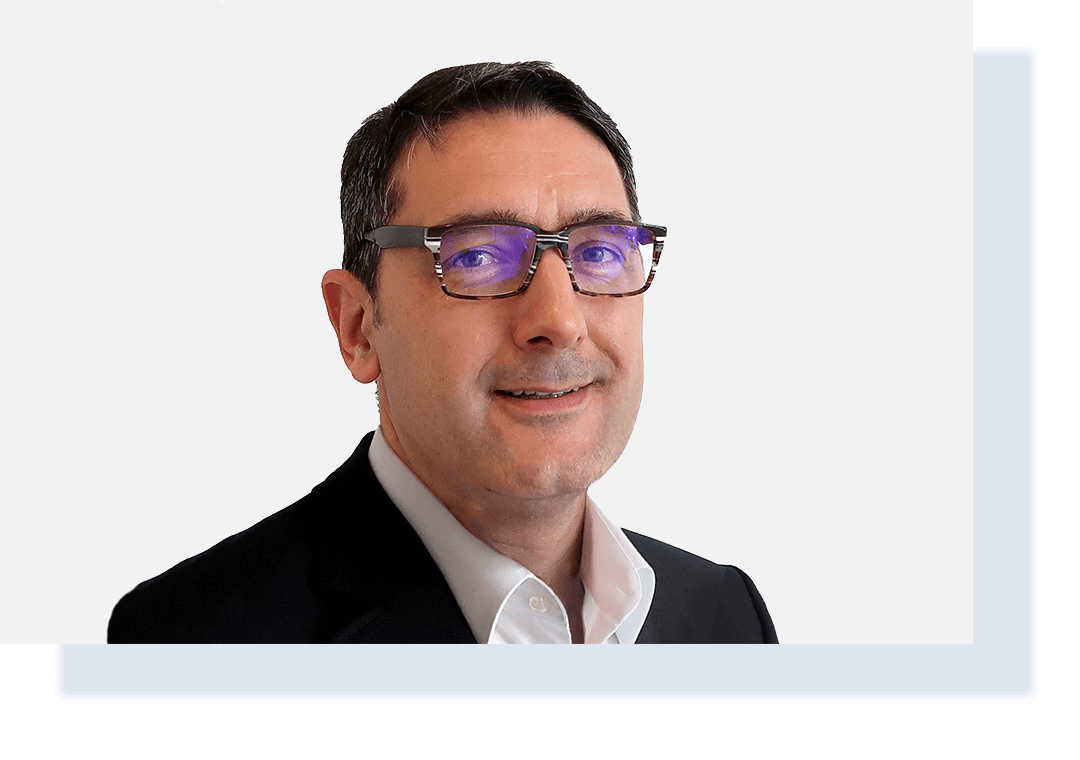